The Evolution of Cement in Prefabricated Building Panels
01.07.2025
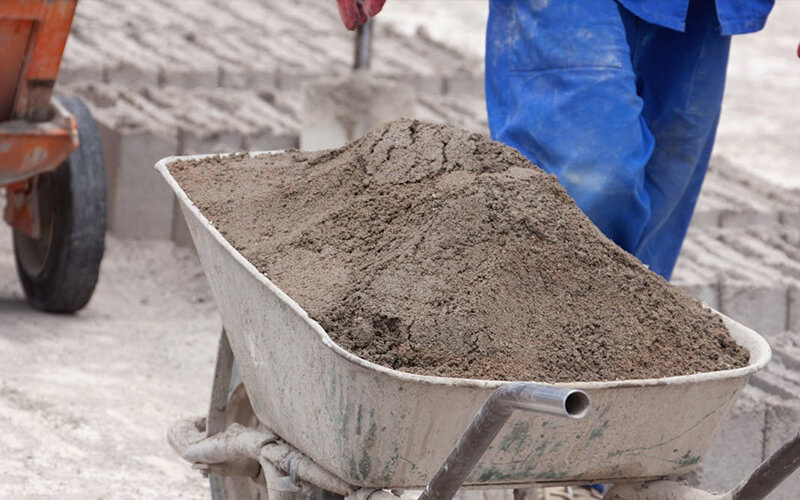
Prefabricated building panels have revolutionized modern construction, offering speed, efficiency, and precision that traditional methods struggle to match. At the core of many of these systems is cement, a material that has continuously evolved to meet the demands of industrialized building. From simple cast-in-place applications to advanced composite panels, cement has played a transformative role in shaping the prefabrication landscape.
This article explores how cement has evolved in the context of prefabricated building panels. We'll examine its historical use, modern innovations, and the future possibilities that make cement a key player in prefab architecture.
Early Use of Cement in Prefabrication
The history of prefabrication dates back to the early 20th century, when builders sought faster ways to assemble homes and commercial structures. Cement was used primarily in the form of precast concrete blocks and panels, created off-site and transported to the construction location. These early products were basic in design but served as the foundation for more sophisticated systems.
Standardization of panel dimensions and production methods in post-war housing projects further accelerated the adoption of cement in prefabricated construction. These panels were durable and fire-resistant, offering a reliable alternative to wood or brick structures that required more labor and time to assemble.
The Rise of Precast Concrete Panels
As prefabrication gained popularity, the industry moved toward more refined cement-based products — especially precast concrete panels. These were manufactured in controlled factory environments, ensuring consistent quality, dimensional accuracy, and surface finishes. The increased strength of modern concrete mixes allowed for thinner, lighter, and more versatile panels.
By the late 20th century, precast concrete panels had become a standard component in commercial buildings, multi-family housing, and infrastructure projects. They could be customized for load-bearing or non-load-bearing applications and integrated with insulation, reinforcement, and surface treatments to meet specific project needs.
Types of Cement-Based Prefabricated Panels
Today, the prefabricated construction sector utilizes a variety of cement-based panels tailored for different applications. Key panel types include:
1. Precast Concrete Sandwich Panels
These panels consist of two outer layers of precast concrete with insulation sandwiched in between. They offer excellent thermal performance while maintaining structural integrity. Ideal for exterior walls, they combine strength, durability, and energy efficiency.
2. Fiber Cement Panels
Made by reinforcing cement with cellulose fibers, these panels are lightweight, flexible, and resistant to moisture and fire. They are commonly used for cladding, ceilings, and partition walls in both residential and commercial structures.
3. Autoclaved Aerated Concrete (AAC) Panels
AAC panels are made from cement, lime, sand, and aluminum powder, which reacts to form air pockets. These panels are lightweight and provide excellent insulation, making them suitable for both load-bearing and non-load-bearing applications.
4. Ultra-High-Performance Concrete (UHPC) Panels
UHPC panels are made with specially formulated cement mixes that provide superior strength, durability, and resistance to environmental damage. They allow for thinner designs and greater architectural freedom in prefabricated systems.
5. Cement-Composite Panels
These are hybrid panels that combine cement with polymers, resins, or recycled materials to achieve specific mechanical or aesthetic properties. They are ideal for decorative façades and interior finishes.
Advantages of Cement in Prefabricated Panels
Cement-based prefabricated panels offer a variety of benefits that contribute to the growing appeal of off-site construction. These advantages include:
- Strength and Durability: Cement provides excellent compressive strength and long-term durability, making panels resistant to wear, weather, and fire.
- Design Flexibility: Modern cement technologies allow panels to be molded into virtually any shape or texture, supporting innovative architectural designs.
- Thermal Performance: Cement panels can be combined with insulation materials to create energy-efficient building envelopes.
- Sound Insulation: Dense cement panels help reduce sound transmission between rooms and from the exterior.
- Fire Resistance: Cement is naturally non-combustible, providing crucial safety in residential and commercial structures.
- Speed of Construction: Prefabricated cement panels minimize on-site labor and weather delays, reducing total project timelines.
Sustainability and Environmental Considerations
As the construction industry faces pressure to reduce its environmental impact, the role of cement in prefabricated panels is being redefined. Manufacturers are increasingly adopting sustainable practices and alternative cement formulations. Some of the key sustainability efforts include:
- Low-Carbon Cements: The use of supplementary cementitious materials (SCMs) like fly ash, slag, and natural pozzolans reduces reliance on clinker, the most carbon-intensive component of cement.
- Carbon Capture and Storage (CCS): Emerging technologies are allowing factories to capture and reuse CO₂ generated during cement production.
- Waste Minimization: Prefabrication reduces on-site waste, and cement panels can often be recycled or reused at the end of their lifecycle.
- Energy Efficiency: Cement panels with integrated insulation lower heating and cooling demands in buildings, contributing to long-term carbon savings.
These innovations are helping cement-based panels align with global sustainability goals and green building certifications such as LEED, BREEAM, and WELL.
Technological Innovations in Cement Panel Production
Technological advancements continue to reshape the way cement panels are produced and applied. Some of the most promising innovations include:
- 3D Printing: Cement-based 3D printing is being used to produce custom panel shapes and decorative elements with minimal waste.
- Automation and Robotics: Robotic arms and automated molds ensure precision and consistency in panel fabrication.
- BIM Integration: Building Information Modeling (BIM) software allows for precise planning and coordination of prefabricated panels in complex projects.
- Self-Cleaning and Photocatalytic Coatings: These surface treatments applied to cement panels help reduce maintenance and improve air quality.
Such innovations not only increase the efficiency of production but also enhance the overall performance and aesthetics of prefabricated cement panels.
Case Studies: Real-World Applications
Prefabricated cement panels are used in a wide range of building types around the world. Notable case studies include:
- High-Rise Residential Towers: In urban areas, precast sandwich panels speed up construction and ensure thermal efficiency for large apartment buildings.
- Educational Facilities: Schools and universities benefit from quick installation and durable finishes offered by cement composite panels.
- Healthcare Buildings: Cement panels are ideal for hospitals due to their fire resistance, hygiene, and acoustic properties.
- Public Infrastructure: Transportation terminals and government buildings often use decorative fiber cement panels for aesthetic appeal and longevity.
These examples demonstrate the versatility of cement in meeting diverse architectural and performance requirements in prefabricated environments.
Challenges and Future Directions
Despite its many advantages, there are still challenges associated with the use of cement in prefabricated panels. These include:
- High Embodied Carbon: Cement remains an energy-intensive material, though low-carbon alternatives are being developed.
- Transportation and Handling: Precast cement panels are heavy, requiring specialized equipment and logistics planning.
- Standardization Issues: The diversity of panel systems can complicate supply chains and project coordination.
The future of cement in prefabrication will depend on continued innovation, regulatory support, and market demand for sustainable and efficient construction methods. Research into carbon-negative cement, advanced composites, and circular economy models will drive the next generation of prefab solutions.
Conclusion
The evolution of cement in prefabricated building panels reflects the broader transformation of the construction industry toward speed, sustainability, and performance. From simple blocks to advanced engineered panels, cement has proven its adaptability and resilience over time. As technology progresses and sustainability becomes a central concern, cement will continue to play a vital role in the future of prefabricated architecture.
By embracing innovation and responsible material sourcing, builders, architects, and manufacturers can leverage cement’s full potential in creating structures that are not only efficient and affordable but also resilient and environmentally sound.