Cement Blends for Harsh Climate Construction Projects
08.07.2025
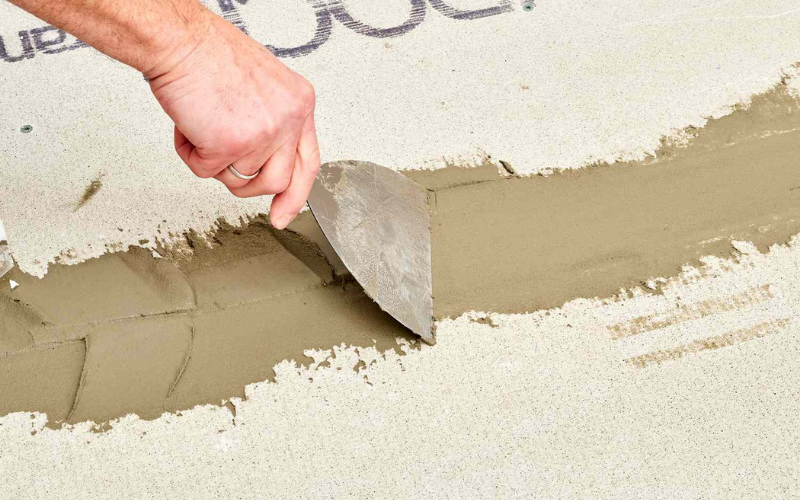
Construction in harsh climates presents unique challenges that demand materials engineered for extreme conditions. From freezing temperatures and high humidity to intense heat and salt-laden environments, traditional building components may fail without proper adaptation. Cement, being a core component in most construction projects, must be formulated specifically to meet the environmental stressors of these regions.
Cement blends have evolved to provide greater resilience, longevity, and performance in climates that push structures to their limits. This article explores the types of cement blends designed for extreme climates, their benefits, and how they contribute to the success of demanding construction projects.
1. Challenges of Building in Harsh Climates
Projects in harsh climates—such as deserts, polar regions, coastal areas, or mountainous terrain—face conditions that accelerate deterioration. Freeze-thaw cycles, saltwater corrosion, UV exposure, and high thermal expansion can cause cracking, spalling, and loss of structural integrity.
Conventional cement types may not offer adequate protection or performance in these environments. Therefore, choosing the right blend of cement is crucial for durability, safety, and cost-efficiency over a building’s lifetime.
2. The Role of Specialized Cement Blends
Specialized cement blends are engineered by modifying the composition of ordinary Portland cement (OPC) or combining it with supplementary cementitious materials (SCMs). These modifications improve properties such as thermal resistance, chemical durability, and mechanical strength.
Blended cements can be tailored to resist specific environmental stressors while also meeting regulatory standards and sustainability goals. Their use helps reduce maintenance needs and enhances the lifespan of infrastructure in demanding settings.
3. Cement Types Suited for Cold Climates
In cold regions, structures must endure multiple freeze-thaw cycles. Water within concrete can freeze and expand, causing internal stress and cracking. To counter this, specific cement blends are used:
- Type III (High Early Strength) Cement: Allows faster curing, reducing the risk of freeze damage before concrete sets fully.
- Air-entrained cement blends: Introduce microscopic air bubbles that absorb pressure from freezing water, preventing internal cracks.
- Low-permeability cement blends: Reduce water penetration, decreasing freeze-related damage.
These cements are commonly used in alpine structures, cold storage buildings, and Arctic installations.
4. Cement for Hot and Arid Climates
In desert or tropical climates, intense heat and rapid moisture loss can lead to plastic shrinkage and thermal cracking. To address these challenges, the following cement blends are used:
- Type II and Type IV Cement: These cements have low heat of hydration, which slows down temperature rise during curing.
- Pozzolanic cement blends: Incorporate materials like fly ash or volcanic ash to improve resistance to cracking and increase workability.
- Cement with hydration retarders: Help prolong setting time, allowing better curing in high temperatures.
Such solutions are essential in the Middle East, parts of Africa, and Southern Asia, where heat can otherwise compromise concrete integrity during construction.
5. Cement Blends for Coastal and Marine Environments
Structures in coastal regions or near saltwater sources face significant risk from chloride attack and sulfate exposure. Salt can penetrate concrete and corrode the steel reinforcement inside, leading to severe structural failures.
The best cement blends for marine applications include:
- Sulfate-resistant Portland cement (Type V): Designed to resist chemical degradation from sulfate-rich soils and water.
- Blends with ground granulated blast furnace slag (GGBS): Provide low permeability and resistance to chloride ingress.
- Silica fume cement blends: Enhance density and impermeability, reducing saltwater penetration.
These cement types are widely used in harbor facilities, sea walls, desalination plants, and offshore platforms.
6. Cement for Seismic and High-Wind Zones
While not climate-specific, areas prone to earthquakes or hurricanes demand additional mechanical resilience from construction materials. In these regions, cement must provide ductility and crack resistance under dynamic loads.
- High-performance concrete (HPC) blends: Include additives that improve toughness and energy absorption.
- Fiber-reinforced cement: Combines cement with steel, glass, or polymer fibers to enhance tensile strength and reduce crack propagation.
These blends ensure that structures can flex and absorb seismic or wind-induced forces without catastrophic failure.
7. Sustainable Cement Blends for Extreme Conditions
Beyond performance, sustainability is now a critical consideration in harsh climate construction. Cement production is a major contributor to global CO₂ emissions, so blended cements offer an eco-friendlier alternative.
- Portland-limestone cement (PLC): Contains finely ground limestone to reduce clinker use and emissions.
- Fly ash and slag cement: Use industrial by-products, improving sustainability and enhancing resistance to heat and chemicals.
- Geopolymer cement: An emerging low-carbon binder that performs well under thermal and chemical stress.
These materials not only endure environmental extremes but also support green building initiatives in vulnerable regions.
8. Application Techniques in Harsh Environments
Even with the right cement blend, proper application is critical. Construction teams must adapt techniques to match environmental conditions, such as:
- Using insulated formwork or heated enclosures in cold climates
- Applying surface curing membranes in hot and windy areas
- Incorporating corrosion inhibitors in marine settings
- Using shrinkage-compensating admixtures for high-temperature projects
Combining the right cement with climate-adapted practices ensures reliable, long-lasting infrastructure.
9. Global Examples of Cement Blends in Harsh Climates
Many iconic structures demonstrate the effectiveness of blended cement in extreme environments:
- The Burj Khalifa (Dubai): Used specially designed concrete mixes with low heat of hydration and high durability under desert conditions.
- The Confederation Bridge (Canada): Spanning icy waters, the bridge incorporates sulfate-resistant cement and air-entrained concrete.
- Offshore oil platforms (North Sea): Built with dense, sulfate-resistant cement mixes to withstand wave impact and saltwater corrosion.
These projects underscore how tailored cement formulations are essential for performance and safety.
10. Choosing the Right Cement Blend for Your Project
Selecting the correct cement blend involves assessing the climate, expected load conditions, and maintenance access. Engineers should work with manufacturers to determine the ideal formulation, often supported by laboratory testing and field trials.
Important considerations include permeability, setting time, shrinkage, and chemical resistance. By aligning material properties with environmental threats, projects can achieve optimal structural integrity and service life.
Conclusion
Cement blends are no longer one-size-fits-all; they are specialized tools tailored to withstand the harshest environments on Earth. Whether it's freezing temperatures, intense heat, or corrosive saltwater, selecting the appropriate blend is essential to building long-lasting, safe, and cost-effective structures.
As climate conditions become more unpredictable and extreme, the role of innovative cement technologies will continue to grow. Investing in the right cement blend today means building resilient infrastructure that stands strong for generations to come.